U.S.A.A.F. RESOURCE CENTER > BOMBERS > SUPERFORTRESS > PREVIOUS PAGE
Design & Development
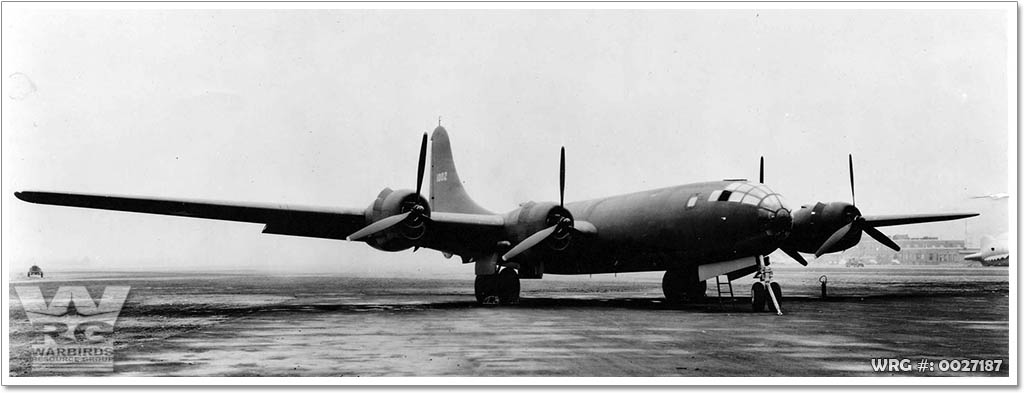
Boeing XB-29-BO, 41-002, the first of three prototypes.
[Source: USAAF Photo]
Manufacturing the B-29 was a complex task. It involved four main-assembly factories: a pair of Boeing operated plants at Renton, Washington (Boeing Renton), and Wichita, Kansas (now Spirit AeroSystems), a Bell plant at Marietta, Georgia ("Bell-Atlanta"), and a Martin plant at Omaha, Nebraska ("Martin-Omaha" - Offutt Field). Thousands of subcontractors were involved in the project. The first prototype made its maiden flight from Boeing Field, Seattle on 21 September 1942. The combined effects of the aircraft's highly advanced design, challenging requirements, and immense pressure for production, hurried development and caused setbacks.

Major sub assemblies of the B-29 Superfortress.
[Source: USAAF Photo]
The most common cause of maintenance headaches and catastrophic failures were the engines. Although the Wright R-3350 Duplex-Cyclone radial engines later became a trustworthy workhorse in large piston-engined aircraft, early models were beset with dangerous reliability problems. This problem was not fully cured until the aircraft was fitted with the more powerful Pratt & Whitney R-4360 "Wasp Major" in the B-29D/B-50 program, which arrived too late for World War II. Interim measures included cuffs placed on propeller blades to divert a greater flow of cooling air into the intakes which had baffles installed to direct a stream of air onto the exhaust valves. Oil flow to the valves was also increased, asbestos baffles installed around rubber push rod fittings to prevent oil loss, thorough pre-flight inspections made to detect unseated valves, and frequent replacement of the uppermost five cylinders (every 25 hours of engine time) and the entire engines (every 75 hours).
Pilots, including the present day pilots of the Commemorative Air Force’s Fifi, one of the last two remaining flying B-29s, describe flight after takeoff as being an urgent struggle for airspeed (generally, flight after takeoff should consist of striving for altitude). Radial engines need airflow to keep them cool, and failure to get up to speed as soon as possible could result in an engine failure and risk of fire. One useful technique was to check the magnetos while already on takeoff roll rather than during a conventional static engine-runup before takeoff.
In wartime, the B-29 was capable of flight at altitudes up to 31,850 feet (9,710 m), at speeds of up to 350 mph (560 km/h) (true airspeed). This was its best defense, because Japanese fighters could barely reach that altitude, and few could catch the B-29 even if they did attain that altitude. Only the heaviest of anti-aircraft weapons could reach it, and since the Axis forces did not have proximity fuzes, hitting or damaging the aircraft from the ground in combat proved difficult.
Defensive gun turret emplacements
The General Electric Central Fire Control system on the B-29 directed four remotely controlled turrets armed with two .50 Browning M2 machine guns each. Some turrets were made according to patents from the Tucker Gun Turret. All weapons were aimed optically with targeting computed by analog electrical instrumentation. There were five interconnected sighting stations located in the nose and tail positions and three Plexiglas blisters in the central fuselage. Five General Electric analog computers (one dedicated to each sight) increased the weapons' accuracy by compensating for factors such as airspeed, lead, gravity, temperature and humidity. The computers also allowed a single gunner to operate two or more turrets (including tail guns) simultaneously. The gunner in the upper position acted as fire control officer, managing the distribution of turrets among the other gunners during combat. The tail position initially had two .50 Browning machine guns and a single M2 20 mm cannon. Later aircraft had the 20 mm cannon removed, and sometimes replaced by a third machine gun.
In early 1945 Major General Curtis Lemay, commander of XXI Bomber Command — the Marianas-based B-29-equipped bombing force — ordered most of the defensive armament and remote-controlled sighting equipment removed from the B-29s under his command. The affected aircraft had the same reduced defensive firepower as the atomic mission-intended Silverplate B-29 airframes, but could carry greater fuel and bomb loads as a result of the change. The lighter defensive armament was made possible by a change in mission from high-altitude, daylight bombing with high explosive bombs to low-altitude night raids using incendiary bombs. As a consequence of this requirement, Bell Atlanta (BA) produced a series of 311 B-29Bs that had turrets and sighting equipment omitted, except for the tail position, which was fitted with AN/APG-15 fire control radar. This version could also have an improved APQ-7 "Eagle" bombing-through-overcast radar fitted in an airfoil shaped radome under the fuselage. Most of these aircraft were assigned to the 315th Bomb Wing, Northwest Field, Guam.
First fully pressurized bomber design
The crew enjoyed, for the first time in a bomber, full-pressurization comfort. This first-ever cabin pressure system for an Allied production bomber was developed for the B-29 by Garrett AiResearch. The nose and the cockpit were pressurized, but the designers were faced with deciding whether to have bomb bays that were not pressurized, between fore and aft pressurized sections, or a fully pressurized fuselage with the need to de-pressurize to drop their loads. The solution was a long tunnel over the two bomb bays so as not to interrupt pressurization during bombing. Crews could crawl back and forth between the fore and aft sections, with both areas and the tunnel pressurized. The bomb bays were not pressurized.
Sources:
Gunston, Bill - The Encyclodepia of the Worlds Combat aircraft, 1976, Chartwell Books, Inc., New York
U.S.A.A.F. RESOURCE CENTER > BOMBERS > SUPERFORTRESS > PREVIOUS PAGE